塑化不***的现象
1. 塑料层表面有皮式现象:塑料层的表面出现一层类似皮革的质感,这通常是由于塑料未能充分塑化导致的。
2. 温度控制较低:仪表指针显示温度低,实际测量温度也低,导致塑料未能达到适宜的塑化温度。
3. 塑料表面发乌:塑料表面颜色变深,失去原有的光泽,这可能是由于塑化不均匀或温度控制不当造成的。
4. 有微小裂纹或未塑化***的小颗粒:塑料中存在明显的微小裂纹或未能完全熔化的小颗粒,这表明塑化过程不充分。
5. 合胶缝合不***:塑料层之间存在明显的接缝或缝合痕迹,这是由于塑化不均匀或模具设计不合理导致的。
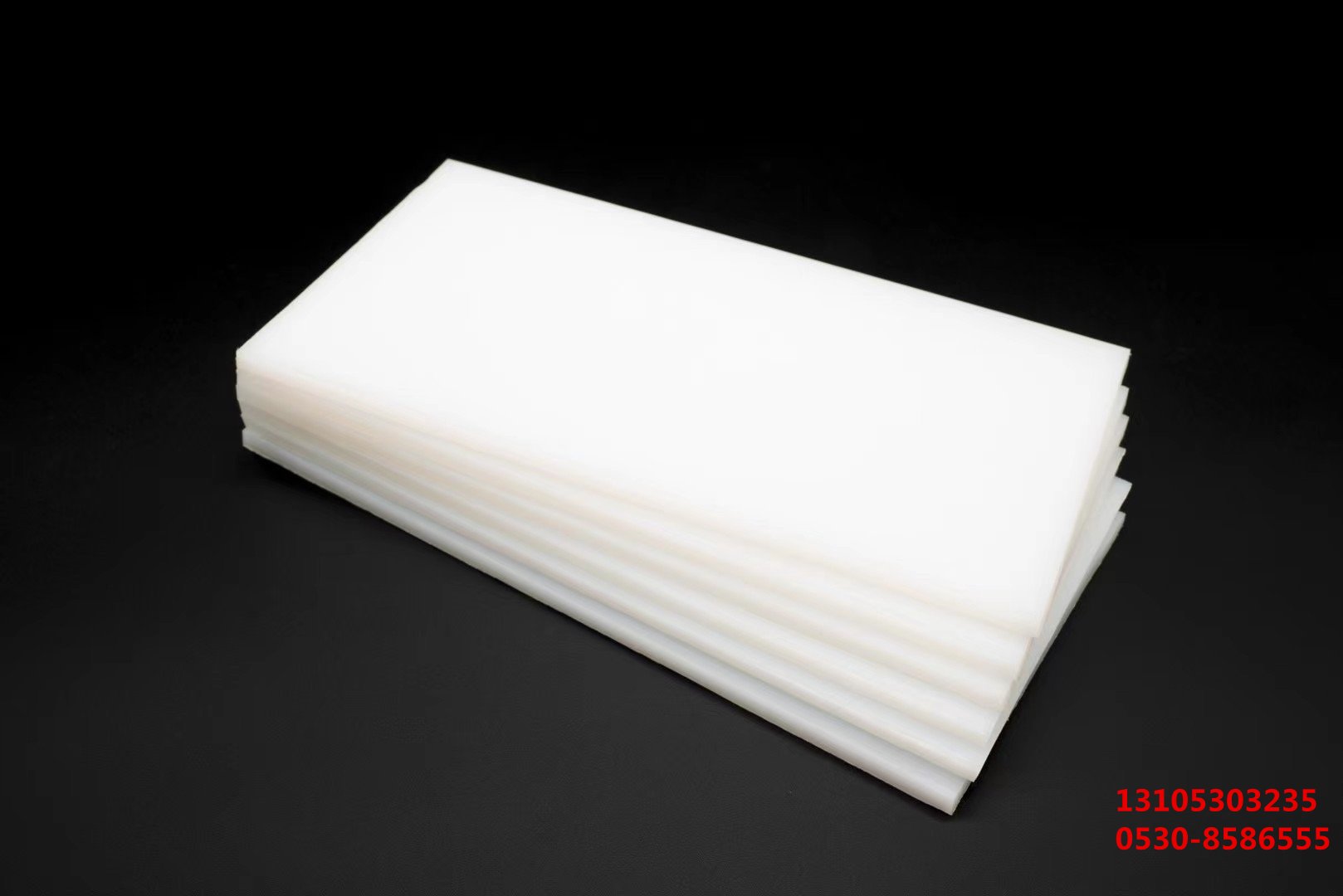
塑化不***的原因
1. 温度控制问题:
温度控制过低或不合适:如果料筒温度、模具温度或注射压力等工艺参数设置过低或不合适,会导致塑料无法充分塑化。
温度控制不均匀:加热系统故障或温控系统失灵可能导致料筒内温度分布不均匀,从而影响塑料的塑化效果。
2. 塑料原料问题:
含有难塑化的树脂颗粒:如果塑料原料中含有难塑化的树脂颗粒或其他杂质,这些颗粒可能无法在设定的温度和压力下充分熔化。
塑料混合不均匀:造粒时塑料混合不均匀或塑料本身存在质量问题,也会导致塑化不***。
3. 设备问题:
螺杆和牵引速度太快:螺杆转速过快或牵引速度过快可能导致塑料在料筒内停留时间过短,无法充分塑化。
螺杆压缩比不合适:螺杆的压缩比过***或过小都可能影响塑料的塑化效果。
模具设计不合理:浇口和流道尺寸过小、模腔内熔料流动路径过长或有薄壁区域等都可能导致塑化不***。
综上所述,PP塑料板厂家在生产过程中需严格控制工艺参数、确保原料质量,并定期维护设备,以减少塑化不***现象的发生,提高生产效率和产品质量。