1. 板材表面出现条纹、气泡或尺寸不一致
模具问题:模具设计不合理,导致料流不均匀,从而在板材表面形成条纹;模具温度控制不当,可能使熔融的PP材料在模腔内冷却速度不一致,进而产生气泡或导致板材尺寸不稳定。
挤出机故障:挤出机的螺杆磨损不均,会使物料挤出量不稳定,影响板材的尺寸精度和表面质量;温控系统失效,导致熔融温度波动,也可能引起板材表面出现条纹或气泡。
2. 板材冷却不均、变形或翘曲
冷却速率不一致:冷却水流量不足、冷却水温度高或冷却装置布局不合理,都会使板材不同部位的冷却速度不同,从而产生内应力,导致板材冷却不均、变形或翘曲。
生产线速度不匹配:如果生产线各环节的速度设置不合理,如挤出速度与牵引速度不协调,也会导致板材在冷却定型过程中受到不均匀的力,进而引起变形或翘曲。
3. 板材厚度公差控制不准确
设备磨损:长期使用的生产设备,如挤出机的螺杆、模具等部件会出现磨损,导致板材的厚度发生变化,难以控制在规定的公差范围内。
测量与控制系统误差:厚度监控系统的精度不够,或者测量传感器出现故障,无法实时准确地监测和反馈板材的厚度信息,从而使操作人员难以对生产过程进行***调整,导致厚度公差控制不准确。
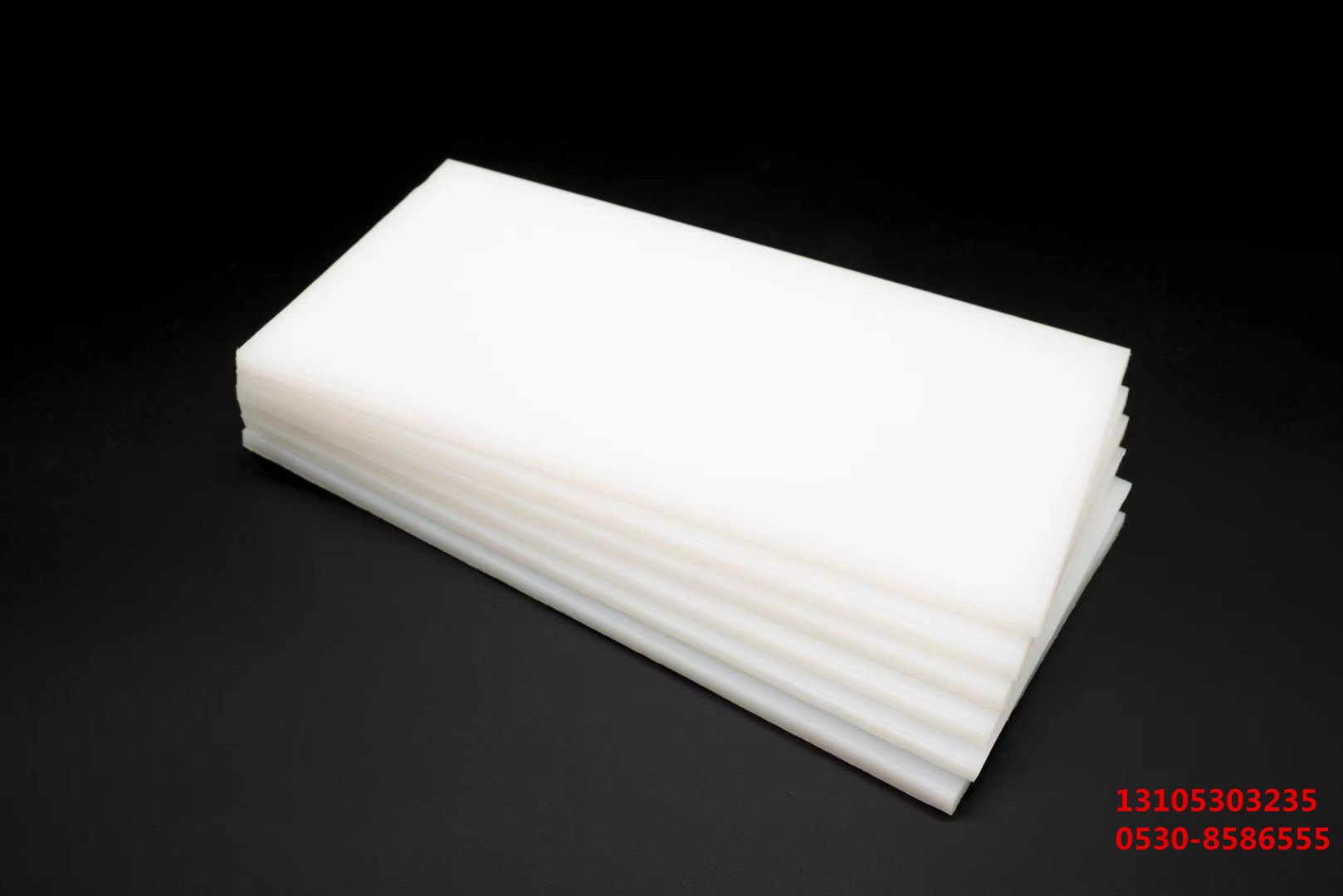
4. 原料供应不稳定
供应商因素:原料供应商提供的材料质量不一,可能存在颗粒不均匀、杂质较多等问题,影响PP塑料板的质量和性能。
存储条件不当:原料存储环境不符合要求,如湿度过高、温度不适等,可能导致原料受潮、变质或降解,进而影响生产过程和产品质量。
5. 挤出机故障
挤出量不稳定:螺杆磨损严重、滤网堵塞等原因,会导致物料的输送和挤出量不均匀,影响板材的连续性和质量稳定性。
塑化不充分:挤出机的加热温度不够或螺杆结构不合理,可能使PP材料未能充分熔融塑化,导致板材内部存在未熔颗粒或晶点,降低产品的物理性能和外观质量。
6. 颜色和光泽度不稳定
色母粒质量问题:使用的色母粒质量不佳,颜色分布不均匀,或者与PP树脂的相容性不***,容易导致PP塑料板的颜色和光泽度出现差异。
生产工艺参数波动:生产工艺参数如温度、压力、速度等的不稳定,会影响色母粒在PP材料中的分散效果和反应程度,从而导致颜色和光泽度的不稳定。
7. 生产线速度不匹配
设计不合理:生产线的设计存在缺陷,各工序之间的衔接不顺畅,导致物料的流动和加工过程出现问题,影响生产效率和产品质量。
自动控制系统故障:自动控制系统的准确性和可靠性不高,无法实时监测和调整生产线的运行状态,使得各环节的速度难以保持同步和稳定,进而影响产品的质量一致性。
综上所述,PP塑料板厂家在生产过程中可能会遇到多种现象,这些现象的产生往往与原材料质量、设备状况、工艺参数、生产环境以及人为操作等多种因素有关。厂家需要针对这些问题采取有效的措施,如加强原材料检验、***化设备维护与管理、严格控制工艺参数、改善生产环境以及提高员工技能水平等,以确保PP塑料板的质量和生产效率。